Prototype 1 Testing
- Nurdle GDP
- May 26, 2023
- 2 min read
By Sowmi Aravinthan
On the 22nd March, the Nurdle Project went to Shamrock Quay in Southampton to test our first prototype called “The Nurdle Nabber V1” (NNV1).
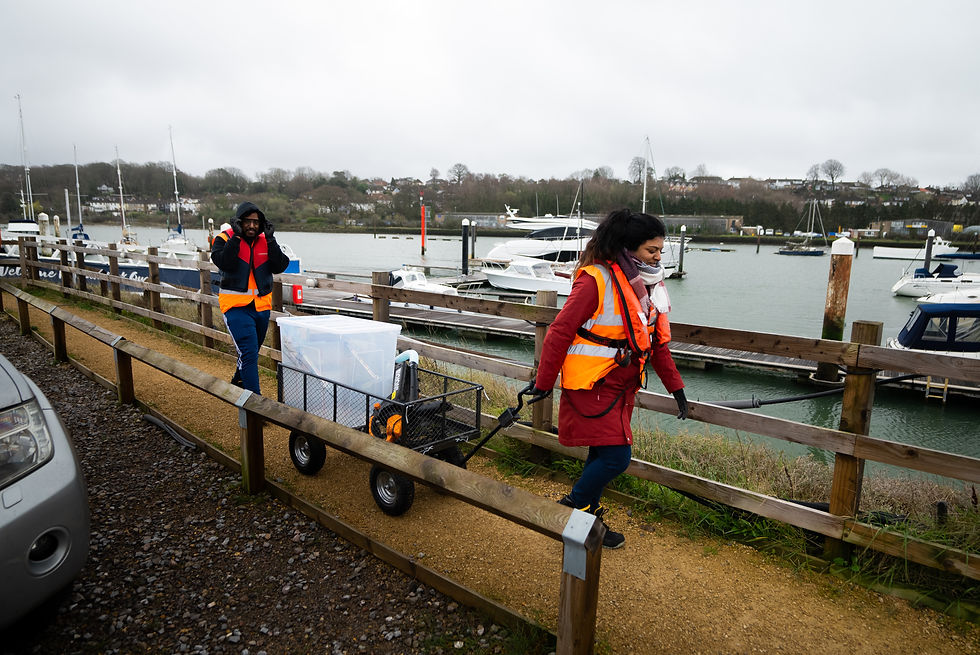
This prototype (shown below) combines the collection and separation systems that we had been working on in our sub-teams, to operate continuously and simultaneously. The collection system consists of an adapted leaf-blower with a Venturi nozzle inside the T-junction, which transports material through a tube to the separation box. The material then enters the separation chamber through an inlet near the top of the box in line with a foam board to reduce the kinetic energy of the material coming in. It will then fall and be sorted by the system of parallel meshes which are attached internally by a spring to create the correct amount of vibration (as found from the angled sieving tests). Sand falls straight through both meshes and is expelled out of the bottom of the box, nurdles and large debris are then separated by the different sized apertures of mesh with nurdles falling into the middle compartments, and debris into the container at the end. For easy removal and changing of container, the meshes are mounted on a pivot and the springs can be easily unclipped.

The actual test took place at Shamrock Quay, on the bank of the river Itchen, which is known for being one of the most polluted rivers in the UK. Although the riverbank was made of mostly mud and gravel, which is not the substrate that NNV1 was designed for, the team went forward with the test as it would be valuable to see how the machine behaved in a real world environment instead of in the lab. As expected, the test provided lots of insight and made clear which part of the system needed refining.

The key observation was that the two systems when combined worked well and sorted nurdles as expected. However, there were some limitations, namely:
- Ergonomics: three people were required to operate the machine as the leaf blower could not be attached to the box and the tube was too inflexible
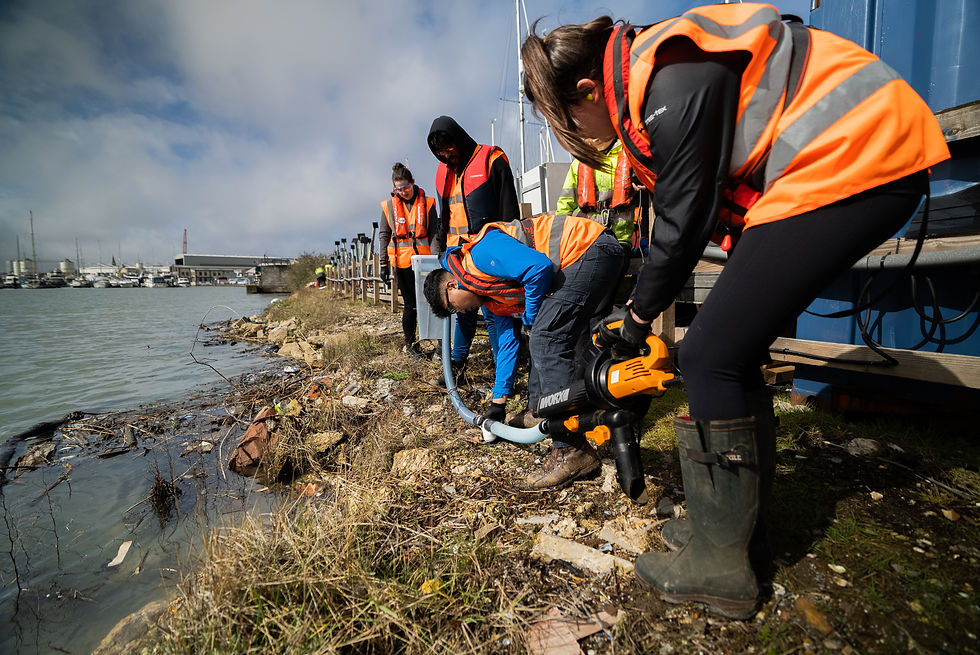
- Fitting of components within separation chamber: the small mesh inside the separation chamber did not have enough support which lead to a bow shape forming where the nurdles got stuck
- Escaping nurdles: bumps and uneven panels on the box made it impossible to completely seal the chamber

Comments